超级电容设计
超级电容模块作为电源到底盘电机中间的功率控制模块,要求完成以下任务:限制电源的输出功率,做到功率实时监控和动态调整;利用电机组功率消耗的谷值时间给超级电容组充电,以达到能量合理分配和利用的目的;实时汇报给操作手超级电容当前电量,方便操作手进行调整。
目录:
一、需求确定
1.1、总体需求
超级电容模块作为电源到底盘电机中间的功率控制模块,要求完成以下任务:
1、限制电源的输出功率,做到功率实时监控和动态调整。
2、利用电机组功率消耗的谷值时间给超级电容组充电,以达到能量合理分配和利用的目的。
3、实时汇报给操作手超级电容当前电量,方便操作手进行调整。
1.2、具体需求
电路主要分为三个大类:1、电源线路 2、检测线路 3、控制电路。
1、电源线路
Ⅰ.BUCK降压转换器:通过控制转换器输出电压来限制输出功率,达到控制输入功率目的(必需)
Ⅱ.BOOST升压转换器:将电源升压给超级电容充电(必需)
Ⅲ.各个芯片的供电电源模块(必需)
2、检测线路
Ⅰ.电流检测模块:总的输入和输出电流(必需)
Ⅱ.电压检测模块:输入电压,输出电压和超级电容电压(必需)
3、控制电路
把检测电路得到的数据输入给STM32芯片,通过运算输出控制量
Ⅰ.计算输入和输出功率(必需)
Ⅱ.使用输入功率与当前等级的限制功率比较,计算BUCK转换器的PWM的占空比(必需)
Ⅲ.使用电容电压计算其剩余电量,发送给操作手,由他控制超级电容放电(必需)
Ⅳ.使用输出功率与一定值作比较,和电容电压共同控制超级电容的充电(必需)
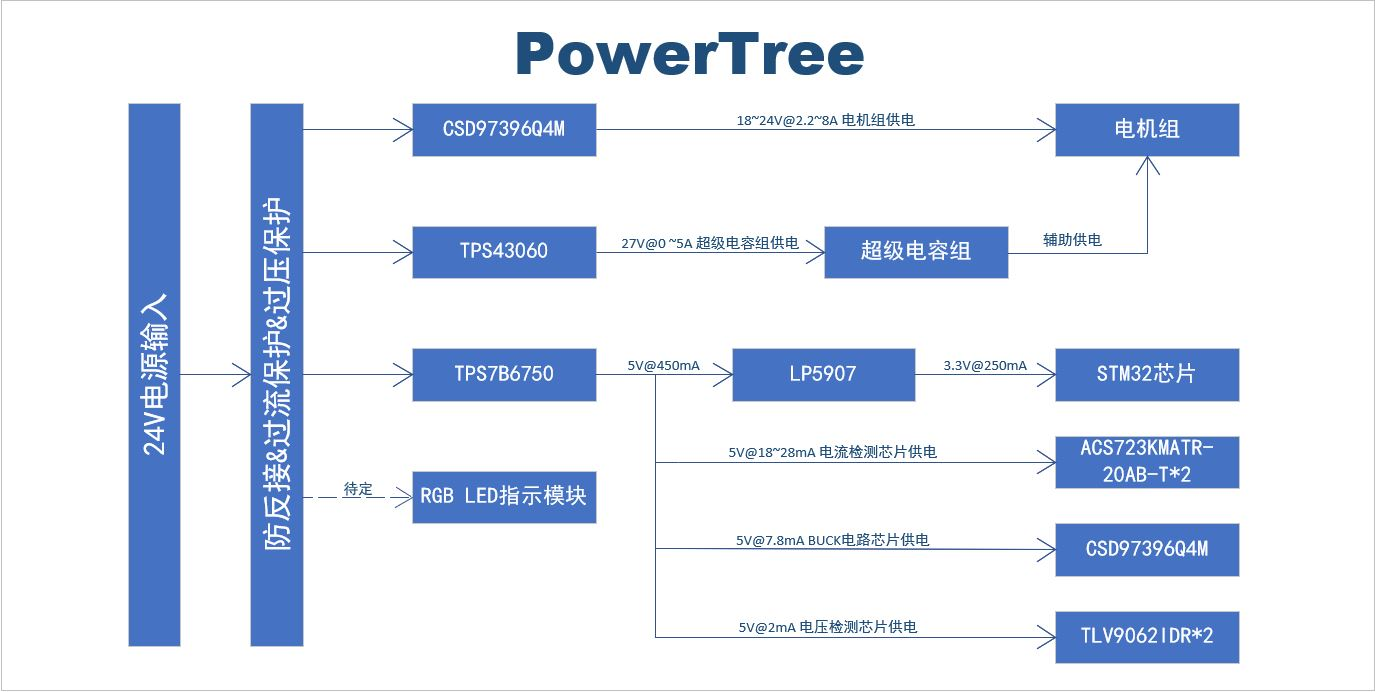
二、电路参数实际计算
2.1、效率分析
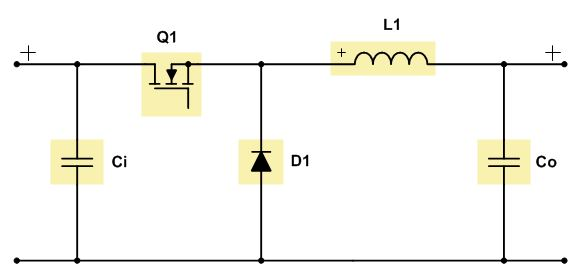
测试电路采用非同步BUCK电路,输出电压值18~24V,测试频率1kHz,负载连接一个无刷直流电机,预计转换效率在95%左右(仿真结果)。实际转换效率75%左右,同时电压有明显波动,但对电机的运动未造成巨大影响(也可能受实验参数限制,未观察出影响)。
分析:由于测试所使用电路相当简单,不存在电路本身结构造成功率损失的问题。于是将问题矛头指向MOS管,二极管和电感这三个元件造成的损耗。测得MOS管IRFP250N的 $R_{DS(ON)}$ 在75mΩ左右,二极管10A10的 $V_F$ 最大为1V,铁氧体芯电感(双1.2线,10mH)的DCR在110mΩ左右。
计算MOS管的损耗:
MOS管在1KHz频率下的主要损耗为:
其中 $P_{CON}$ 为导通损耗,为开通损耗, 为关断损耗。
$P_{CON}$ 的计算通式为(取占空比的中间值的导通损耗为准):
和的计算过程若是较真起来会相当复杂,这里先采用近似最坏假设计算:
其中 $V_{DS}$ 为导通压降, $I_{DS}$ 为平均电流, $T_r$ , $T_{d(ON)}$ , $T_f$ 和 $T_{d(OFF)}$ 分别为上升时间,开通延迟时间,下降时间和关断延迟时间。
总损耗:
计算二极管的损耗,这里以二极管的最大损耗为准:
其中 $V_F$ 为导通压降, $I_F$ 为导通电流,D为占空比
计算电感的损耗:
电感的铜损:
其中 $I_F$ 为导通电流,DCR为电感直流电阻
电感的铁损:
注意:这里的公式是大量简化后得到的,同时忽略了涡流损耗,原因是电感体积较小,具体分析根据文献[1]。实际计算公式是基于 Steinmetz方程修正得到的,但该修正方程的参数难以获得,故使用简化方程。
假设电路工作在CCM(电流连续)模式下,仍然以占空比中间值计算,则:
$B_{PP}$ 为磁通变化量,D为占空比,T为周期,N为匝数, $A_e$ 为磁芯横截面积, $U_i$ , $U_o$ 分别为输入电压和输出电压,f为频率
综上,可知二极管的损耗是最大的,是由其不可忽略的导通压降带来的。但,这不意味着其它两个元件的损耗也是可以忽略的,我必须认识到,这里的频率只有1kHz,属于低频。根据MOS管计算损耗的公式可知,其损耗会随着开关频率的升高而升高,具体体现在开通损耗和关断损耗 ,虽然现在这两个值可以忽略不计,但我要往高频化方向发展时,这两个量会变得相当可观。根据电感计算损耗的公式,同样可知,其损耗也会随频率的升高而升高。庆幸的是,根据文献[1],铁损在占空比D大于0.5的情况下损耗低于小于0.5的情况。
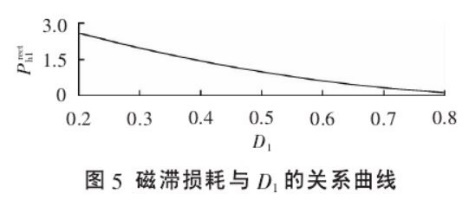
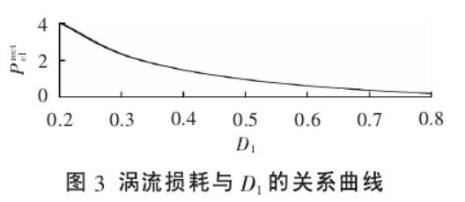
要说明的一点,电感的损耗计算可能误差会较大,市面上的电感本身标称误差就在±20%,且电磁场也是让分析变得难上加难。不过无妨,分析的过程本身是绝对正确的,可以一定程度反应实际情况,方便指导今后工作。而且,我在下面会介绍更好的器件损耗计算方法。
最后,不通过计算,还有一种方法可以大致得知哪个元件损耗最大,即连通电源和负载后,放在桌面上半个小时,用手摸哪个发烫严重便可判断。
2.2、主要参数计算
查询过多方资料,得知这种非同步BUCK转换器的转换效率普遍不高,做得好的一般在80%以上。最后,在TI公司的资料里了解到同步BUCK转换器,通过替换二极管为MOS管大幅度减低导通压降。改进方案:
1、将电路替换为同步BUCK电路。控制难度会有所提升,但采用TI公司的一些器件可以达到稳定控制。(值得注意的是,同步电路并非完美,它在轻负载的情况下造成了不良的电路反应,即在高侧MOS管关断时,电感电流可能会倒流,但使用二极管不存在该问题,因此我选用的芯片有二极管仿真模式,价格也相对合理。)
2、提高开关频率,可以减小电感体积,提高能量密度,改善动态响应。(换用外径20mm的电感,原来的为31mm。)
3、采用软开关技术,减小由提高频率带来的开关损耗增加的问题。(尚未考虑周全,且计划先提升至10kHz,不算高频。)
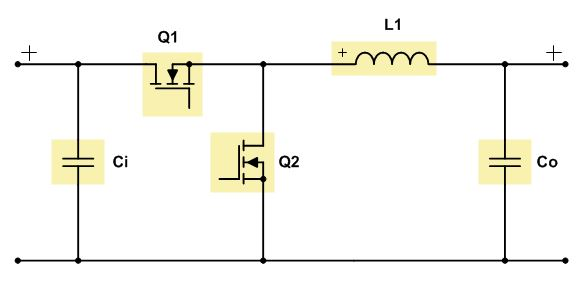
DC-DC转换电路外围电感选型需要考虑以下几个参数:
电感量L:L越大,储能能力越强,纹波越小,所需的滤波电容也就小。但是L越大,通常要求电感尺寸也会变大,DCR增加,导致DC-DC效率降低,相应的电感成本也会增加;
自谐频率 $f_0$ :由于电感中存在寄生电容,使得电感存在一个自谐振频率。超过此f0是,电感表现为电容效应,低于此 $f_0$ ,电感才表现为电感效应(阻抗随频率增大而增加);
直流电阻DCR:指产品电极之间所用漆包线的总的直流电阻,根据 $W=I^2R$ ,DCR可造成能量损耗, 降低DC-DC效率,也是导致电感发热的主要原因;
交流电阻RAC:指电感量在指定频率下的电阻值,主要由电感线圈的直流电阻(交流下的集肤效应)、磁芯损耗以及介电损耗等组成,RAC越大,Q值越小;
饱和电流 $I_{sat}$ :通常指电感量下降30%时对应的DC电流值;
温升电流 $I_{rms}$ :通常指是电感表面温度上升40℃时的等效电流值;
这里我主要考虑L,DCR, $I_{sat}$ 和 $I_{rms}$ ,优先选择L,后三个主要和所用线的线径有关。
电感
电感值选用规则和计算公式:
当MOS管打开时,电感电流线性上升,当MOS管关断时,电感电流线性下降,电感电流最大和最小值之差为电感纹波电流,该值也可以用输出负载电流乘以一个电流纹波系数r表示,即:
r一般在 0.3~0.5 之间。这里,我引入了一个重要的参数电流纹波系数r。为什么在算电感量之前要引入该参数?因为我要明确告诉后来人,这个参数远比电感值本身重要。
电流纹波系数r(参考文献[3])定义:
式(2-2-2)表示了电感电流的交流分量与直流分量的几何比例。其中 $∆I = 2 \ast I_{AC}$ ,一旦r确定,其他的所有参数几乎都能确定,因此,r值一定要清晰理解,仔细选择。
电流纹波率r只适用于连续导通模式,有效值范围为0~2。显然,r=0时,电感无穷大,电流无波动,r=2时,转换器处于临界导通模式。我们当然希望输出的电流和电压都能平稳,所以,r值的取值便更偏向于取小(r并非越小越好)。
在功率变换的计算中,我们通常用伏秒积表示电感在开关管开通关断过程中能量守恒。将式(2-2-3)代入式(2-2-2),得式(2-2-4)(2-2-5):
其中 $I_L$ 为电感电流, $V_{ON}$ 为开关管开通时的电感电压, $V_{OFF}$ 为关断时电感电压
最后,说明为何这个系数如此重要——因为它是基础量。实际情况中,L的取值由工况,开关频率,甚至是拓扑本身决定的。因此无法直接计算L。但是存在r值的一般设计经验,并已被广泛应用。
任何情况下,r值都在0.3~0.5之间,其通常最优值为0.4,但不绝对,我就选了0.2。原因:电感尺寸没办法继续缩小了,纹波率太大反而增大滤波电容体积。(注:内容繁多,这只是相当简单的介绍,攫取了其中能快速解决问题的知识。)
按照式(2-2-5)选择电感值,这里为最大占空比计算值,对于BUCK电路,存在固有的最大占空比 $D_{max}$ ,实际计算时选择两者中的较小值。
以上电感值是计算值最小值,随之得到的饱和电流 $I_{Lrms}$ 和峰值电流 $I_{Lpeak}$ 是最小值。按照工程上的要求,考虑到市面上的电感的标称值的误差通常在±20%,还考虑到当电感电流达到饱和电流时,电感值会下降25%,即:
因此,我们只要选用比 $L_{chosen}$ 大的,满足峰值电流 $I_{Lpeak}$ 条件的电感。最后我决定选用2mH 1.2线的功率电感(DCR=11.55mΩ)。
电感损耗计算:
此外,我还推荐TI公司的一款软件Power Stage Designer Tool 4.0,该软件提供了相当全面的电路图。TI毕竟是业界的龙头,开关电源做得很好,很多资料都可以参考他们的。
电容
输入、输出滤波电容选用规则和计算公式(参考文献[2]),输出电容参数分析:
$C_o$ 很大的话,可以保证输出电压近似恒定,但是$C_o$很大会导致体积和成本更大。因此实际中根据容许的输出电压纹波来选择 $C_o$ 的值。设计时总是按照电感电流谐波全部进入 $C_o$ ,恒定分量进入负载(如果带阻性负载,在闭环电路的控制下,输出电压恒定,确实是这样的)。电感电流i的谐波进入电容,由电容的寄生电阻ESR、寄生电感ESL,和$C_o$值决定电压纹波的。
对于低于500kHz的谐波,ESL产生的电压纹波可以忽略。因此,输出电容中由ESR和 $C_o$ 决定纹波电压分量。由ESR产生的纹波分量正比于电感电流纹波分量,由 $C_o$ 决定的纹波分量与流过电容的电流积分成正比。这两个分量相位是不同的。
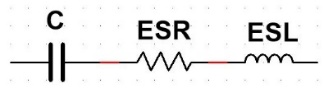
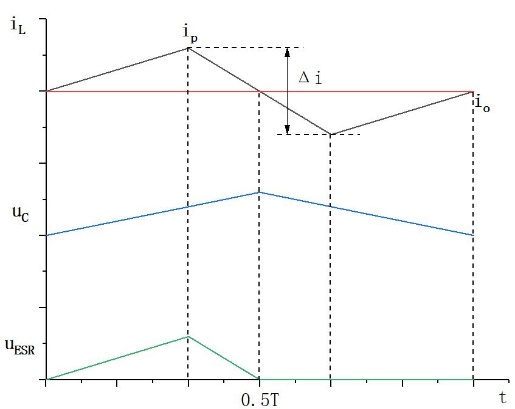
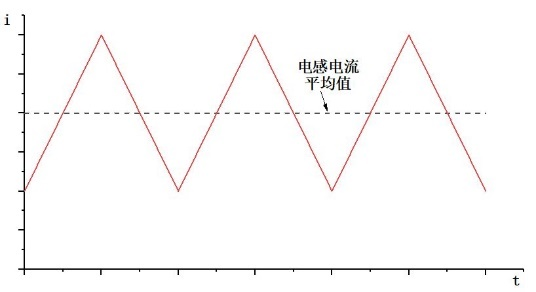
对于BUCK,BOOST和BUCK-BOOST,其输出电容的最大有效值电流恰好都对应同一电压,而且该电压就是一般电感设计步骤中采用的电压值。即,对应BUCK的 ,BOOST和BUCK-BOOST的 。因此,可直接使用由一般电感设计步骤的计算值。
另外,由于电容的ESR值对开关电源来说是一个很重要的值,过大会造成严重的电压尖峰,电容发热,电容失效等问题。通常,普通铝电解电容的ESR会达到欧姆级别。这里,我均选用贴片固态铝电解电容的ESR值(50mΩ:大致包括导线)计算。
输出电容参数计算:
此处设置的任务是同时满足下述三个约束条件(可自行调节)。
(1)最大输出纹波峰峰值小于输出电压的1%,即
(2)负载突增时,可接受的最大电压下垂量为: $∆V_{DROP} = 1.175V$ ;
(3)负载突增时,可接受的最大超调量为: $V_{OVERSHOOT} = 1.175V$ ;
先计算选用的电感后的电流纹波率(式(2-2-12))和输出电流纹波峰峰值(式(2-2-13)):
得出电容寄生电阻ESR最大值,基于最大输出纹波:
根据图2,电感电流在平均值以上的部分为滤波电容充电,其面积为 $∆S$ ,输出电容充电量 $∆Q$ ,根据能量守恒, $∆S= ∆Q$ ,通过式(2-2-15),(2-2-16),得到式(2-2-17):
同时,当负载发生变化时,假定输出电压需要2到3个开关周期返回到正常输出值,这段时间内不希望电压跌落至某一值。由 $I = C \frac {di}{dt}$ ,基于最大电压下垂量,可得式(2-2-18):
此处的下垂量与额外负载需求相关,因为正常负载需求在每个周期里都会被满足,电压不会下降。所以,此处的电流实际上对应增加的负载。
最后,基于最大超调量,采用另一个标准:负载从最大负载$I_o$突变至0,所有的电感能量倾泻到输出电容中,升压到 $V_X$ ,同样,根据能量守恒,由式(2-2-20)推导出式(2-2-21)。
输出电容损耗计算:
输出电容有效值电流计算:
功耗计算:
输出电容损耗取最恶劣情况做参考。
综上,理论的输出电容值 $C_o$ 为400uF,值得说明的一点,以上的计算均为理论推算,参数也有选取上的偏差。但是,不妨碍我们选电容,理论为400uF,我们可以选470uF的电容,也可以选用两个220uF并联,甚至是多个并联,这里,我推荐后一种,这样就算是高ESR电容,两个并联也可以有效减小ESR值,同时耐压值比最大电压高出20%~50%。我选择330uF 50V贴片固态电解电容,三个并联。
输入电容参数计算:
输入电容一般要保证输入电压纹波峰峰值保持在输入电压的5%~10%以下,因此输入电容也会影响BUCK电路的工作稳定性。由于我们是使用锂电池,所以这个输入电压纹波值较小。不过还是给出一个值:要求输入电压纹波峰峰值为2%,同时也是防止电压纹波从输出端口传递到输入端口造成干扰。假设输入电压最高时,纹波最大。将式(2-2-27)(2-2-28)求得输入电压纹波峰峰值和最大输入电压下,对应输出电压的占空比代入式(2-2-29)。
输入电容损耗计算:
输入电容有效值电流计算:
其中与计算 $C_o$ 时的是一样的,与同理(上述两式对应两种 $U_o$ )
输入电容损耗取最恶劣情况做参考。
因此,我选择82uF 35V贴片固态电解电容,两个并联。容的种类繁多,开关电源电路推荐多层式陶瓷电容(MLCC),固态电容,钽电容,铝电解电容。推荐度按顺序递减,自己查阅相关参数便会明白原因。
最后,必须要说明的一点,对于BUCK和BUCK-BOOST电路,输入电容的最大有效值电流出现在D=0.5,对于BOOST电路,这个值是1,但是工程上占空比不超过0.9。因此,上述计算的取值都是偏向D=0.5。以上便是超级电容主要的设计思路和理论分析过程。
参考资料:
[1] 周岩,张俊波,陈麒米.开关变换器功率电感磁损建模及应用[J]. 电力自动化设备,2017,37(11):132-135.
[2] 马文超. BUCK电路外围器件参数选型分析[J]. 电子与封装,2019,19(12):30-31.
[3] Sanjaya Maniktala.Switching Power Supplies A-Z,2E[M]. Beijing: The Posts and Telecommunications Press,2015:47-80.